Steel is one of the most common materials available today. It is a combination of iron and carbon in a certain percentage. There are many variations of this material, since even slight changes in its chemical composition can alter its physical and mechanical properties. The raw materials for steel production today are represented by waste steel products. Production of structural steel from cast iron has also been established.
The best Steel Fabricators in the steel industry produce billets according to standards. Let’s take a look at the features of steel fabrication as well as the methods used.
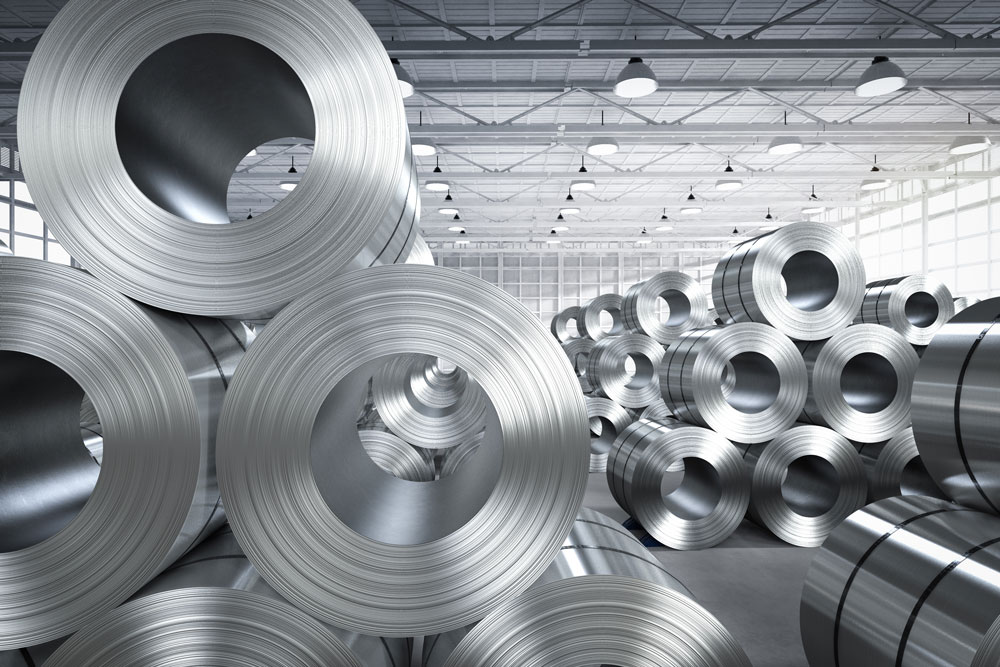
Peculiarities of the steel manufacturing process
In the production of cast iron and steel different technologies are used, despite the rather similar chemical composition and some physical and mechanical properties. The difference lies in the fact that steel contains fewer harmful impurities and carbon, due to which high performance qualities are achieved. In the smelting process, all the impurities and excess carbon, which cause the material to become more brittle, are lost in the slag. The technology of steel production involves forced oxidation of the main elements through the interaction of iron with oxygen.
Considering the process of producing carbon and other types of steel, there are several major steps in the process.
- The melting of the rock. The raw material that is used to produce the metal is called the charge. At this stage, the oxidation of iron involves the deoxidation of impurities. Much attention is paid to ensuring that the concentration of harmful impurities, which may include phosphorus, is reduced. In order to provide the most suitable conditions for the oxidation of harmful impurities, a relatively low temperature is initially maintained. The iron slag is formed by the addition of iron ore. After the harmful impurities are released on the surface of the alloy, they are removed, and a new portion of calcium oxide is added.
- Boiling of the obtained mass. The baths of molten metal are heated to a high temperature after a preliminary purification stage of the composition, and the alloy begins to boil. Due to boiling, the carbon in the composition begins to actively oxidize. As noted earlier, cast iron differs from steel due to too high concentration of carbon, which makes the material brittle and acquires other properties. Such a problem can be solved by blowing in pure oxygen, due to which the oxidation process will proceed at high speed. When boiling, carbon monoxide bubbles form, to which other impurities also adhere, making the composition cleaner. At this stage of production, sulfur, which is one of the harmful impurities, is removed from the composition.
- Compound deoxidizing. On the one hand, the addition of oxygen to the composition provides the removal of harmful impurities, but on the other hand it leads to a deterioration in the basic performance. That is why the diffusion deoxidation, which is based on the introduction of a special molten metal, is often carried out to clean the composition from harmful impurities. This material contains substances that have about the same effect on the molten alloy as oxygen.
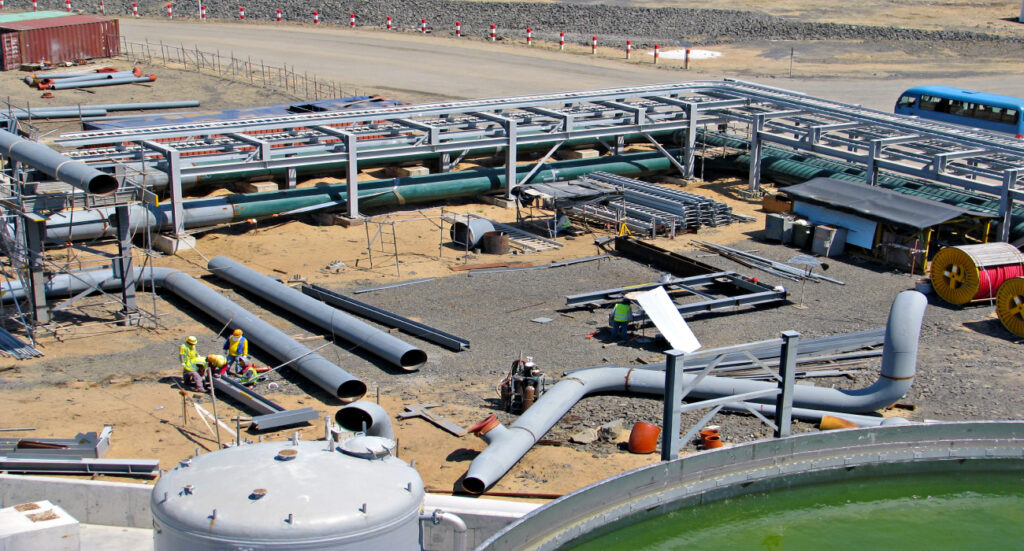
Methods of making steel
There are several methods of making steel, each has its own specific advantages and disadvantages. The chosen method determines what properties the material can be produced with. Let’s look at the main methods of metalwork melbourne.
- Siemens-Martin process. This technology involves the use of special furnaces, which are able to heat the raw material to a temperature of about 2000 degrees Celsius. Considering the methods of production of alloy steels, we note that this method also allows the addition of various impurities, which make it possible to obtain an unusual composition of steel. The Siemens-Martin process is based on the use of special furnaces.
- The electric arc furnace method. In order to obtain high quality material, steel is produced in electric furnaces. By using electric energy to heat the raw material, it is possible to accurately control the oxidation process and the release of slag. In this case, it is important to ensure that the slag is produced. They are a transmitter of oxygen and heat. This technology reduces the concentration of harmful substances such as phosphorus and sulfur. Electric smelting can take place in a wide variety of environments: overpressure, vacuum, in a certain atmosphere. Research indicates that electric steel has the highest quality.
- Oxygen-converter. Continuous casting of steel in this case is accompanied by active oxygen injection, which significantly accelerates the oxidation process. This manufacturing method is also used to produce cast iron. It is believed that this technology is the most versatile and makes it possible to produce metals with different properties.